補修事例
お客様から寄せられた補修事例の一部
主な事例
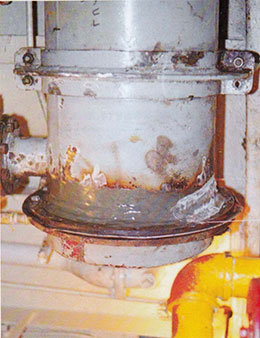
クラック補強
メインエンジンのフレッシュウオータークーラーの表面にクラックが数力所できて、穴があいて漏れが生じた。この例では、表面処理をしたあと縦型ボディーに対して補強テープを用いて、ベロメタルを塗布。これに要した時間。50分未満で、結果はきわめて良好なものでした。
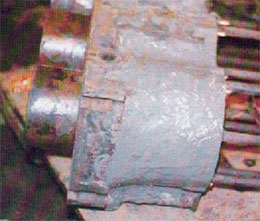
ひび割れ補修
航海中船舶のディーゼルエンジンのブロックのあちこちにひび割れが起こり、合計30ケ所の修理を行った。まず表面を粗し、クリーナーで洗浄処理を行い、そのあと、穴を薄い銅で覆った。その上にベロメタルを塗布して補修。約3時間後にエンジンの油圧テストを実施したが、テスト結果は万全のものでした。
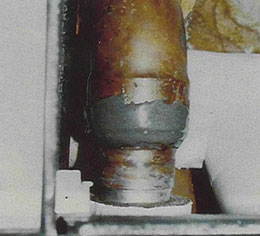
ウォーターラインの補修
口径10cmのコンデンサーウオーターラインの補修を行ました。補修には約20分間の時間を要した。従来の修理工法に比べて、ベロメタルの補修効果で約¥300,000節約が出来た。投資金額は初回の補修のみで充分ペイ出来るものです。
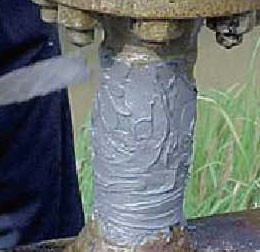
マニホールド部分の補修
口径46cmのトランクラインの口径5cmのマニホールドの部分の補修部位を撮ったものです。このもれは現場の作業員が誤って弓のこで切り落としてしまったもので、他の工法では4つのステーションに1日当たり50,000b流すのを止めざるを得ないところでした。ベロメタルを使用して、実際には工事は2時間以内で終える事が出来ました。
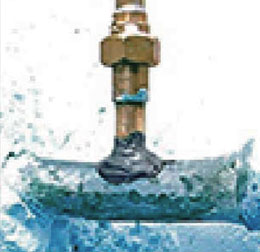
貯水槽の補修
主にS02のダクトのガス漏れとリードタイプの水漏れを防ぐ為に、速乾タイプのベロメタルを使用しました。大口径の77cmのS02が通っている鋼管のガスダクトと水を溜めるリードウオーターの貯水槽の補修を行ました。この補修の結果、他のエ法よりも機器の停止時間を数時間費用で¥150,000相当の天然ガスの使用料を節約できました。
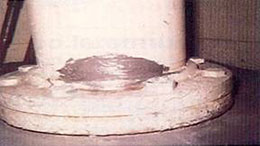
火災用スプリンクラーの補修
全プラントに関係する火災用のスプリンクラーシステムの直径 26cmのメインパイプの漏れ止めを30分で行ました。従来の方法ではかなりの経費が掛か以稼働停止時間が7時間は必要でした。その間は火災の危険にさらされていたということになります。
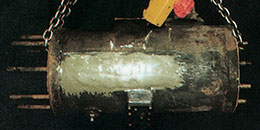
ガスエンジンシリンダの補修
ベロメタルで補修したガスエンジンシリンダで、コスト 3万円、稼働停止時間で約8日間を節減することができました。
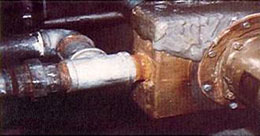
ポンプケースの補修
ポンプケースの補修をしました。稼働の停止時間は24時間を予定していましたが、補修時間は3時間でした。もし代替品を注文したとすれば3週間は必要でした。
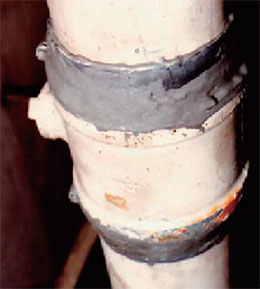
パイプ配管亀裂の補修
冷暖房機のパイプ配管に亀裂が発生したためにベロメタルで補修作業を行ました。問題なく運転再開しています。
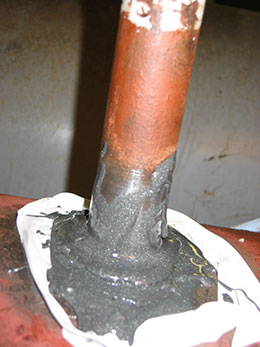
油送管接合部破損の補修
石油タンクと油送管の接合部が破損のため、ベロメタルで補修を行いました。溶接作業では中身を空にして長時間の運転休止に伴う損額も覚悟していましたが、ベロメタルでは簡単に補修作業を終えることができました。